DMLS 3D printing stands for Direct Metal Laser Sintering, this 3D printing technology is famous for printing metal 3d models. Now, if you are thinking of starting with this technology you need to know DMLS 3D printing’s advantages and disadvantages. This article will help you in deciding whether you should go with DMLS 3D printing or not.
The main advantage of DMLS 3D printing is its high strength and durability which makes it ideal for prototype printing and performing tests on the prototype and its main disadvantage is its cost which is comparatively high when compared with FDM and SLS 3D printers. Now, there are many other advantages and disadvantages related to DMLS 3D printing so keep reading.
DMLS 3D Printing In A Nutshell
DMLS stands for Direct Metal Laser Sintering, which is a type of 3D printing technology that uses a laser to fuse metal powders together to create a three-dimensional object.
A 3D CAD model is first created, then it is then divided up into layers. A construction platform is covered with a layer of metal powder, and a strong laser is then used to selectively melt and fuse the metal particles together while adhering to the layer’s 3D model. After the item is finished, the platform is lowered, another layer of powder is applied over the first, and the procedure is repeated.
DMLS can produce highly complex, geometrically intricate metal parts with good mechanical properties and accuracy. It is a popular choice for rapid prototyping, small-batch production, and high-value end-use parts in the aerospace, medical, and automotive industries. The range of materials available for DMLS is also expanding, including various alloys of steel, titanium, aluminum, and cobalt-chrome.
Now, let’s look at DMLS 3D printing’s advantages & disadvantages.
Advantages & Disadvantages of DMLS In A Nutshell
S.No. | Advantages | Disadvantages |
---|---|---|
1. | Design flexibility | High cost |
2. | High accuracy and precision | Limited build volume |
3. | Fast production | Surface finish |
4. | Material Variety | Support structures |
5. | High strength and durability | Material limitations |
6. | Reduced waste | Safety concerns |
DMLS Printing Advantages In Detail
Design Flexibility
DMLS 3D printing offers design flexibility because it can produce highly complex and intricate designs that are difficult or impossible to achieve with traditional manufacturing methods. It enables the creation of parts with internal channels, lattice structures, varying wall thicknesses, and other intricate shapes that are challenging to produce with conventional machining.
This design freedom leads to more innovative and optimized products that meet specific application needs.
High Accuracy & Precision
DMLS 3D printing technology offers high accuracy and precision, which is another key advantage of the technology. DMLS can produce parts with tolerances as low as a few microns, allowing for parts with precise dimensions and high accuracy.
It uses a high-powered laser to selectively melt and fuse metal particles together, following the shape of the layer as defined by the 3D model. This allows for precise control over the deposition of the material, which results in parts with high accuracy and precision.
Additionally, DMLS can produce parts with smooth surfaces and sharp details, ensuring that parts meet exact specifications and requirements. This level of accuracy and precision is particularly useful for producing complex or intricate parts with tight tolerances, making DMLS a popular choice for industries such as aerospace, medical, and automotive.
Overall, the high accuracy and precision of DMLS 3D printing technology allow for the production of parts with exact specifications and precise dimensions, offering numerous benefits for a wide range of industries.
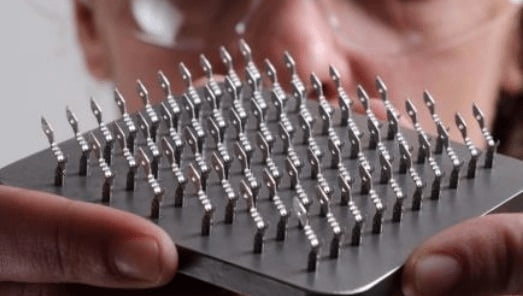
Fast Production
DMLS is a rapid manufacturing process that can produce parts quickly and efficiently, reducing lead times and production costs.
DMLS works by selectively melting and fusing metal particles together, layer by layer, according to the 3D model. This additive manufacturing process allows for the production of complex parts without the need for expensive tooling or molds, which can significantly reduce production time. It can produce multiple parts at once, depending on the size and complexity of the parts, which further reduces production time and costs. This is particularly useful for small-batch production, where traditional manufacturing methods may not be cost-effective.
Material Variety
DMLS can print with a variety of metals, including stainless steel, titanium, aluminum, and more, allowing for the production of parts with different material properties and characteristics.
Each metal material has its own unique properties, such as strength, toughness, and heat resistance, allowing designers to choose the best material for a specific application. Furthermore, DMLS can produce parts with varying material properties within the same part, allowing for the creation of customized parts with unique material characteristics.
DMLS can use powder materials that are recycled, reducing material waste and costs. This is particularly useful for small-batch production, where traditional manufacturing methods may require expensive molds or tooling.
High Strength & Durability
DMLS can produce parts with high strength and durability, making them suitable for demanding applications where parts need to withstand high stress and wear.
DMLS uses a high-powered laser to selectively melt and fuse metal particles together, creating a fully dense and strong part with high mechanical properties. This results in parts with high tensile strength, hardness, and wear resistance, making them suitable for applications in industries such as aerospace, automotive, and medical.
Furthermore, DMLS can produce parts with high dimensional accuracy and consistency, ensuring that parts meet exact specifications and requirements. This level of accuracy and consistency is particularly.
Reduced Waste
DMLS is an additive manufacturing process that builds parts layer by layer, using only the required amount of material for each layer.
This is in contrast to traditional manufacturing methods, which often involve subtractive processes that create significant waste. For example, machining a part from a block of the material may produce a large amount of scrap material that cannot be reused.
Additionally, DMLS can use powder materials that are recycled, further reducing material waste and costs. This is particularly useful for small-batch production, where traditional manufacturing methods may require expensive molds or tooling.
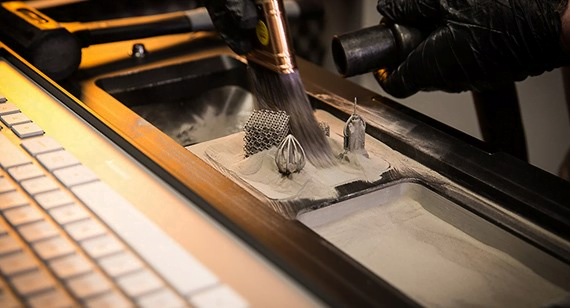
Trending Posts
- DIY Parachute for Drone | 3D Printed Safety System That Saves the Sky
- DIY 80mm EDF And Thrust Test – All Steps
- DMLS 3D Printing Advantages & Disadvantages | Detailed
- 3D Printer Nozzle Issues | Solution & Details
- The Best & Cheapest IDEX 3D Printer | 2022
- 3D Printer Nozzle – Changing And Assembling Them
DMLS Printing Disadvantages In Detail
High Cost
DMLS 3D printing can be expensive due to the high cost of equipment, materials, skilled labor, time, and design complexity. The machines used for DMLS 3D printing are expensive and require regular maintenance. The metal powders used in DMLS 3D printing can be expensive, especially when using specialized alloys. Skilled operators are required to operate and maintain the equipment, which can impact the cost of the process.
The process is slow, especially for large or complex parts, which means that it may require multiple runs or iterations to produce a satisfactory part. Parts with intricate geometries or high levels of detail may require more time, material, and labor to produce, which can add to the overall cost of the process. Despite the high cost, DMLS 3D printing remains a valuable technology for creating metal parts and prototypes with high precision and accuracy.
Limited Build Volume
The build volume of a DMLS machine is typically smaller than other 3D printing technologies, which can limit the size of the parts that can be produced. This can be a challenge for industries such as aerospace and automotive, which require larger parts. However, as the technology continues to evolve, it is likely that DMLS machines with larger build volumes will become available, allowing for the production of larger parts.
Surface Finish
In general, the surface finish of DMLS parts is relatively rough compared to other manufacturing methods, such as CNC machining or injection molding. This is because the process involves melting and fusing metal powders layer by layer, creating a slightly porous surface with visible layer lines.
However, there are post-processing techniques that can be used to improve the surface finish of DMLS parts. For example, parts can be machined, polished, or treated with various coatings or finishes to achieve the desired surface texture and appearance. These additional steps can increase the time and cost of the process but can result in high-quality parts with a smooth and uniform surface finish.
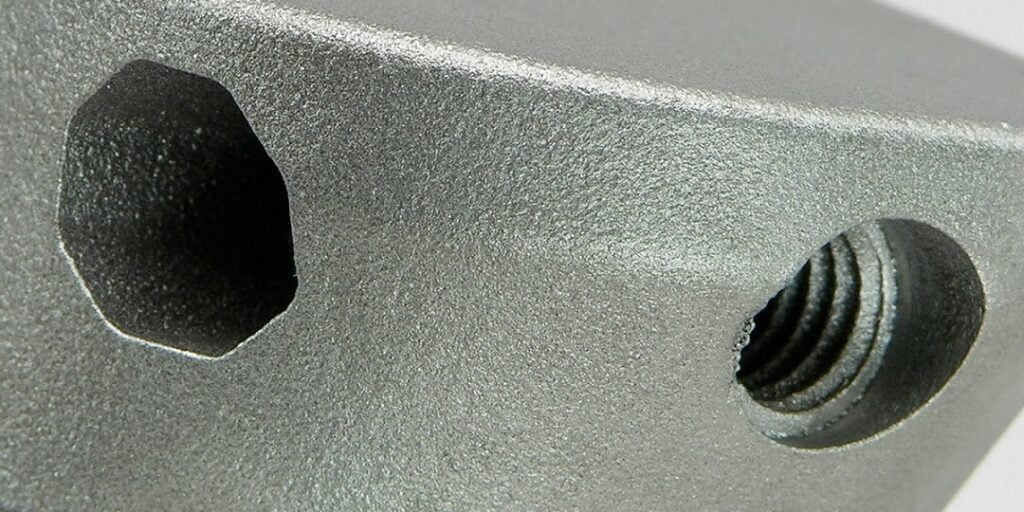
Support Structures
Support structures add to the time and cost of the printing process, as they require additional material and time to be printed and removed after printing is complete. Removing support structures can also be challenging, especially for complex parts or hard-to-reach areas, which can impact the overall quality of the finished part.
In addition, support structures can leave marks or blemishes on the surface of the part where they were attached, which can be difficult to remove or require additional post-processing steps. They can also limit design freedom, as certain features or geometries may require extensive support structures to be printed correctly.
Material Limitations
While DMLS offers many benefits such as reduced lead times, improved design flexibility, and high precision, it also has some materials limitations.
- Material Availability: DMLS is limited to a few types of metal powders, which can limit the variety of materials available for use in DMLS. While materials like stainless steel, titanium, and aluminum are commonly used in DMLS, other metals like copper and nickel alloys are not widely available.
- Powder Quality: The quality of the metal powder used in DMLS is critical to the success of the process. The metal powder must be free of impurities and have a consistent particle size to ensure a uniform build. Poor powder quality can lead to defects in the finished part and may even damage the printer.
Safety Concern
Like any 3D printing process, there are certain safety concerns that need to be considered when using DMLS 3D printing. Here are some potential safety concerns to keep in mind when using DMLS 3D printing:
- Resin Exposure: The resin used in DMLS 3D printing can be toxic if ingested or if it comes into contact with the skin or eyes. It is important to handle the resin with care and to wear appropriate personal protective equipment (PPE), such as gloves and goggles, to prevent accidental exposure.
- Fire Hazard: The resin used in DMLS 3D printing is flammable and can ignite if exposed to heat or an ignition source. It is important to keep the printing area well-ventilated and to avoid using the printer near open flames or other sources of heat.
- Mechanical Hazards: The moving parts of the DMLS 3D printer, such as the build platform and resin tank, can pose a mechanical hazard if not handled properly. It is important to follow the manufacturer’s instructions for operating the printer and to avoid putting fingers or other body parts near moving parts.
- UV Radiation: The projector used in DMLS 3D printing emits UV radiation, which can be harmful to the eyes and skin. It is important to wear appropriate PPE, such as goggles and long-sleeved clothing, to protect against UV exposure.
- Post-Processing Hazards: After the printing process is complete, the object may need to be post-processed with chemicals or heat to finalize the curing process. These processes can pose additional safety hazards if not handled properly.
DMLS Advantages & Disadvantages: FAQ
What are some material limitations in DMLS 3D Printing?
Material limitations in DMLS 3D printing are that some metal types are easily available like stainless steel, titanium, and aluminum while copper and nickel alloys are not easily available.
What are the safety concerns related to DMLS 3D printing?
Some major safety concerns regarding DMLS 3D printing are resin exposure, fire hazard, mechanical hazard, UV radiation, and post-processing hazards.
What are some major advantages of DMLS 3D printing?
The major advantages of DMLS 3D printing are design flexibility, high accuracy, fast production, reduced waste, etc.
Conclusion
This article on DMLS 3D printing’s Advantages & Disadvantages covers most of the major advantages and disadvantages. Some of them may have been missed, you can point them out in the comments section given below.
Thank You!