Dual Extruder 3D Printer: One of the most interesting and tough questions of the 3D printing world. Most of you have thought about this. We think that having a dual extruder 3d printer will solve our various problems. Problems like printing time, using two types of filaments at once, etc. So, here we are after testing and having to spend a reasonable amount of time, to guide you in the path of a dual extruder 3D printer.
Dual Extruder 3D Printer: Ways to do it.
There are mainly two ways to do this. First, you can make one yourself and second is that you can buy a pre-build dual extruder 3D printer. Well, the second one is obvious, thus we are not going to talk about it.
When our colleagues told us about an extraordinary off-the-self dual extruder kit it definitely took my interest. There is a company by the name of MAKERTECH which sells these dual extruders switching kits at the price of approximately 80 dollars. This kit uses a server to switch between both extruders.
It looked quite good so we ordered one, we have been working with it for few days. It has been working well but there were problems from time to time. There were few problems such as after installations few parts were broken. There was some bug in Merlin software and the calibration was non-ending we have to do it from time to time.
I can say one thing definitely that it is not for beginners or for peoples who don’t understand the working of the 3D printer inch-by-inch. They gave a pretty good instruction manual I’will give these instruction manuals a solid 9 out of 10.
So, now how would you know if your 3D Printer is suitable for this dual extruder addon. We have make a checklist to made it easier for you.
- 20×20 mm V slot gantry to suit the new carriage.
- Your 3D printer should have a large build volume, as using this extension takes on some printing space.
- It senses metal only so, the glass build surface won’t be any good.
- Mainboard with 5 stepper motor outputs.

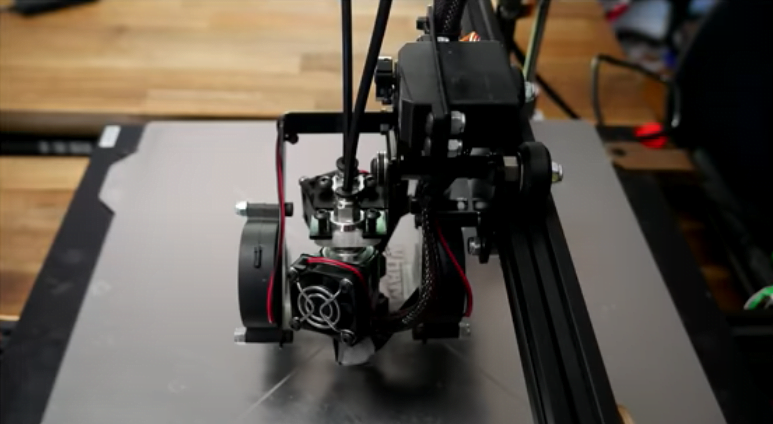

MAKERTECH Dual Extruder kit
Hardware assembly
The kit assumes that you already have one extruder and therefore comes with an additional extruder for you to fit in. Now the hot ends, come with E III D V6 clones.
This means they’re not all metal and the PTFE tube has to travel down inside all the way up to the top of the nozzle. We also noticed the included nozzles was 0.3 millimeter in the orifice. Each hot end assembles exactly the same as an e3d v6 and it wasn’t long until we had both of them together and ready for the printer.
Now for the main feature which is the mechanism for the switching extruders. We start with the servo that needs to fit in through the top, be careful not to damage the wiring. All of the mounting hardware is nicely labeled with correctly scaled images on the back for identification.

M4 nuts and bolts are used in each corner to hold the servo to the bracket. Next, we take the smaller bracket that holds the front cooling fan and we use more M4 nuts and bolts to attach it to the main plate. The two-part cooling blower fans can now be bolted to this assembly lock nuts are used throughout to stop the part from vibrating.
After this, the auto bed leveling sensor goes into the included hole. Now we prepare the bracket that holds the ooze shields and some PTFE tape is included to wrap around and coat the surface.
It’s time to open up and assemble the new carriage. Next, we have a pivoting bracket that holds the two hot ends which swivel on a thrust bearing and bolts to the main bracket. The hole for this seems fairly accessible but we fumbled for quite a while trying to get the washer and lock nut through the inside of the whole thing.

Electrical Assembly
We did our cable management for each of the two hot ends. By cable management, we mean that you need to make sure your cables are long enough to reach when it’s facing straight down, but not so long that the cables get caught when it’s wiggled out of the way. You’ll also need to provide a long enough path for all of the cables wrapped in some sort of sheathing to be secured elsewhere on the printer frame.
Now comes the more serious work the wiring. The wiring for this conversion is a big deal here are all the factory wires and then when we examine the new loom we can see that it’s exactly twice as big. You need to disassemble this box and then feed the old wiring out through the grommet. The old metal connector that used to go into the box for the hot end can no longer be used. There are not enough wires here for two hot ends so you’re going to need to come up with another solution. We used red and green heat shrink over each set of wires so we could tell which one went to the left and right extruder and hot end.
Below is our final wiring chart as per given instructions.

Preparing Dual Extruder for 1st Print
After flashing the firmware we can see that we now have two hot ends shown on the top-left of the LCD display. We can now install the little arm that switches between the two nozzles. Beyond this, there were a series of much simpler final steps like hot tighten nozzles, calibration steps, PID autotunes, spool holder, heat and load filament, and set probe z offset.
After doing all the necessary assembling we can now run a dual extrusion calibration model like the one available on their website. To download and see how close the fit is and tweak our numbers further from there. It took us a few goes to get it spot-on, but our final values were minus 20.2, 0.4, and minus 0.2.
Our final problem was that blobs were being deposited on the model despite the ooze shield. In the worst cases, these would knock the model clear when the next nozzle slammed into them. The instructions state you can bend the shields into place to make sure they’re sealing firmly but this had no effect.
We then noticed during printing that the blob was coming before the tool changes. So it had to be slicer-related MAKERTECH has a custom version of cura if you are using their printer which we were not. In this case, we were using simplified 3d and we started with an inbuilt GTECH a 20M profile. We did things like removing the mixing extruder and then come to the g-code tab and input the correct build dimensions.
But the real problem for us was in the scripts, for the tool change it doesn’t retract but then it tries to move to a new position and Prime before it actually gives the T1 or T0 command to perform the tool change. We ended up stripping out most of that so all it did was the tool change retract and then the T command to switch to the other tool. This completely fixes our problem with the blobs gone and the models no longer being dislodged.
Print Result
This model is very clean in terms of dual extrusion, and we didn’t even need a purge block. It’s satisfying to finally get this working but we’d be lying if we didn’t admit it was a nightmare at times apart from the broken servo and a BL sensor. We’re still a fan of this kit much of the problem solving we had to do was because this extra set wasn’t really intended for our printer.
But instead of a specific model, we’re just getting started on this because this setup has a lot of possibilities. You could have dual-color as we’ve seen here, you could have a big nozzle and a small nozzle, you could have multi-material maybe your PLA with the Flex you could print PLA on one extruder and dissolvable support material on another. You could even try the same material from two different nozzles at different temperatures like the foam filament.
Dual Extruder FAQ:-
There are two methods to solve this. The first is to make another extruder kit by yourself which is a very hectic process, other is to assemble a prebuilt dual extruder kit on your 3D printer.
Having a dual extruder 3D printer has many benefits over a single extruder 3D printer like you could print two types of material at once, print two colors of material, have different temperature settings for both the nozzles, etc.
A prebuilt dual extruder 3D printing kit costs around $80 at most. We have personally used MAKERTECHs dual extruder kit which costs us around $75.
So that’s it for the dual extruder 3D printer, if you have any questions feel free to ask in the comments section below. If you liked our work then you could share it with your friends and subscribe to our newsletter. Comment your thoughts on this Dual extruder 3D printer kit by MAKERTECH in the comments section below.