STEREOLITHOGRAPHY or SLA is a growing technology in the 3D printing industry. Most of us start our 3D printing journey with FDM printers as they are easy to work with and maintain. But at some time we want to try other printing technologies and thus we look for SLA 3D printing. We too did that and thus wanted to share with you about the SLA printing working and technology that we have learned in the process.
What is the working principle behind SLA technology? A UV light is used to cure or harden the resin where required, whilst a platform moves the object being made upwards after each new layer is cured. In SLA 3D printing the model is made from bottom to top in an inverted condition.
The term STEREOLITHOGRAPHY was coined by Charles W. Hull in 1986 who patented the technology and used it to find the company 3D Systems and commercializing the process. SLA is a part of the VAT polymerization category. VAT polymerization is a technology that utilizes VAT as well as lasers to cure photopolymer resin.
In The Post:-
- Technology Used In SLA 3D Printers
- Working of An SLA 3D Printer
- FAQ on SLA 3D Printing
- Conclusion
Technology Used In A SLA 3D Printer
Different 3D printing technologies have different ways in which prototypes can be generated and hence the parts or whole mechanisms differ from each other. In this article, we are going to put in front of you information about making SLA prototypes. When it comes to making an SLA prototype, everything starting from the SLA resin, part or functional prototypes, layer thickness and resolution, other considerations, and ways in which you can finish plays a part.
Laser Source
It is the most important equipment used in the SLA 3D printers. The SLA 3D printers use an ultraviolet laser which cures the photosensitive resin in a selective way. The laser is used to harden the modern layer by layer and thus slowly forming the model as a whole.
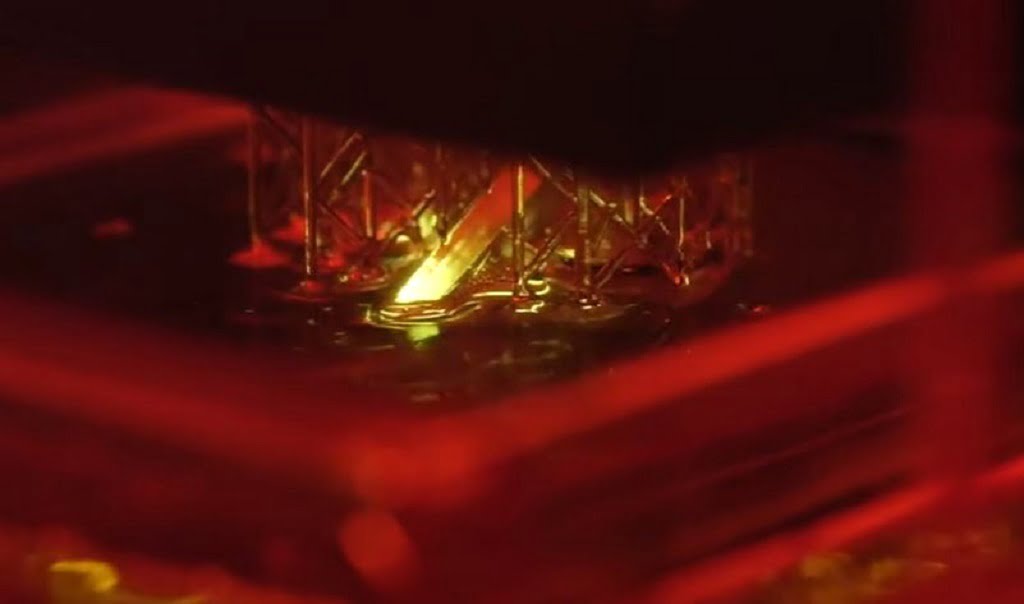
X-Y Scanning Mirror
The laser beam from the source falls on the X-Y scanning mirror and this points the beam on the resin and traces the geometry of the design. This mirror is moved with the help of galvo motors.
Resin Tank (VAT)
This tank holds the photopolymer resin. It also works as an area where the bed moves up and down to make different layers one by one.
UV Curable Resin
This is the liquid photopolymer resin which is UV curable, i.e. it hardens on contact with the ultraviolet laser. It is of different types depending upon the properties of the resin ex. Gray, High-Detail, Mammoth, Transparent Resin, etc.
Cured Layers
These are the solidified resin layers that are cured by the laser. These layers are stuck with the inverted bed. Finishing them one by one we get our finished model.
Build Platform
The layers stick to the movable build platform, which this platform is generally made up of. This building platform moves in the Z-direction while printing. It is positioned such that a very thin layer of resin is allowed beneath it i.e. in the range of 100 microns.
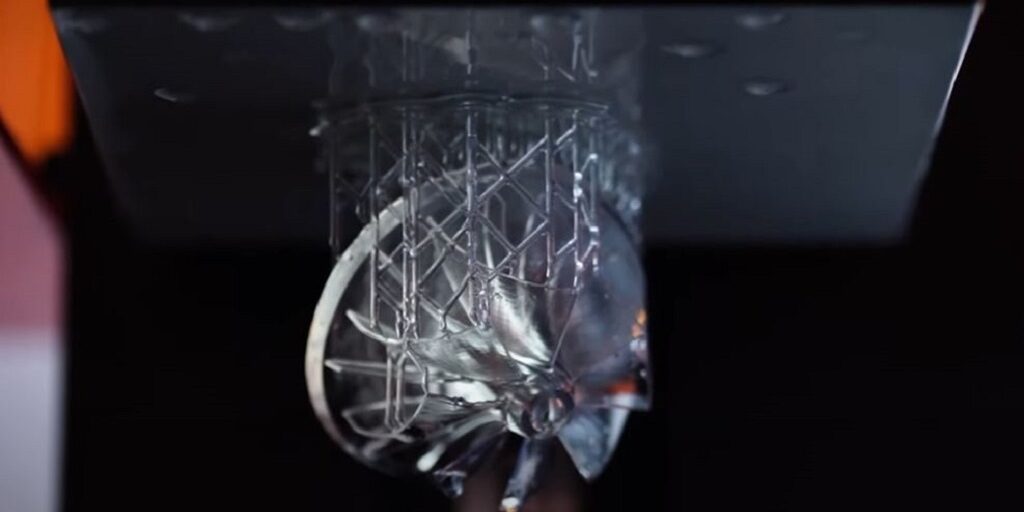
Elevator
The elevator system controls the movement of the build platform in the Z-direction. It is used to move the build platform up and down and also control the layer height.
Working Of A SLA Printer
SLA falls into those classes of additive manufacturing processes that rely on lasers to do the heavy part. Some other technologies which do the same are Selective Laser Sintering and Direct metal laser sintering. The working of an SLA 3D printer can be divided into 4 steps i.e. Printing, Cleaning, Post-Curing, and Post-Processing.
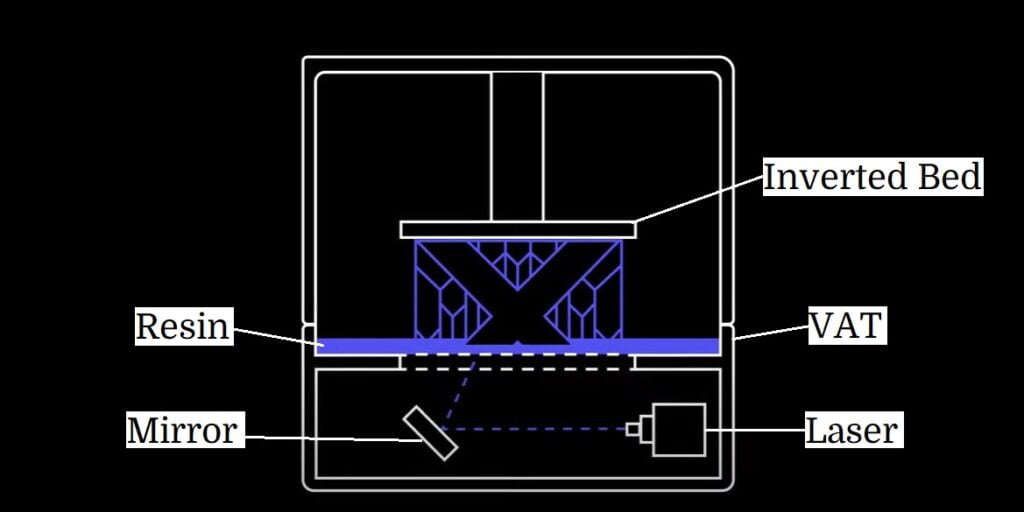
Printing
The SLA Machine begins the 3D printing process by drawing the layers of the support structures (especially in the case of printing overhangs in SLA 3D Printer), followed by the part itself, with a UV light aimed onto the surface of a liquid thermoset resin. The build platform is positioned or dipped in the tank at a distance equal to the height of one layer of the liquid resin.
The UV laser is then activated and falls on the scanning mirror. This mirror directs the laser beam on the resin and traces the X-Y geometry of the design or the cross-sectional area of the model. The resin is cured and it hardens, and the first layer sticks to the build platform.
This completes the first layer of the print. After a layer is imaged on the resin surface, the build platform shifts up and a recoating bar moves across the platform to apply the next layer of resin.
Next, the build platform drops down by one layer height and the laser again activates and traces the geometry of the next layer. The process is repeated layer by layer until the build is complete.
Cleaning
The completed print is lined with the residual resin from the tank. It is still dripping with the sticky resin. So, the build platform is removed from the elevator system manually and is rinsed in isopropyl alcohol (IPA) solution to remove the uncured resin.
Post-Curing
From there, parts undergo a UV-curing cycle to fully solidify the outer surface of the part. It enables the printed parts to attain their full material properties. It is highly recommended for functional parts. After curing, the part functions as per the material properties mentioned by the material manufacturer.
During the curing process, the monomer carbon chains are activated and become solid creating a strong bond between each other. This ‘photopolymerization’ process is irreversible and SLA parts cannot be brought back to their liquid form. This is because SLA materials are made from Thermoset polymers as opposed to thermoplastics used in FDM materials.
Post Processing
The final part of the SLA process is the application of any custom or customer-specified finishing. The support structures can be easily removed and further post-processing like sanding, machining, priming, painting, etc.
FAQ on SLA 3D printing
Engineers, designers, manufacturers, and more choose SLA 3D printing for its fine features, smooth surface finish, ultimate part precision and accuracy, and mechanical attributes like isotropy, water tightness, and material versatility.
The two technologies are typically able to produce parts faster. Because DLP/ LCD 3D printers flash a single image of each layer across the entire platform at once, while SLA flashes a single point. DLP/ LCD 3D printers offer speed that often comes at a cost of precision.
Conclusion
The whole 3D printing industry is now moving towards printers that can produce parts faster than ever before. The resin-based carbon printer claims to be able to produce parts 25 to 100 times faster than traditional SLA by continuously pulling out the part of the resin, rather than printing one layer at a time. So, from the above article, we conclude that
- SLA is perfect for smaller parts, that have intricate details or have a smooth surface.
- Part orientation and support structures play a big impact on the surface finished parts.
- And, there are a lot of materials available in the desktop and industrial spaces.
We are waiting for your feedback on the post. Thank You!